Many sports venues have been used for a period of time. Due to long-term exposure to outdoor conditions and improper maintenance, there will always be some damage. The following small series will introduce how to deal with the crack damage in the silicon pu court.
The course is generally laid on a suitable asphalt or cement foundation. The silicone pu elastic soft surface layer is also used as the floor for indoor and outdoor courts. The construction of a complete silicon pu stadium requires precise planning, analysis, calculation, and preparation.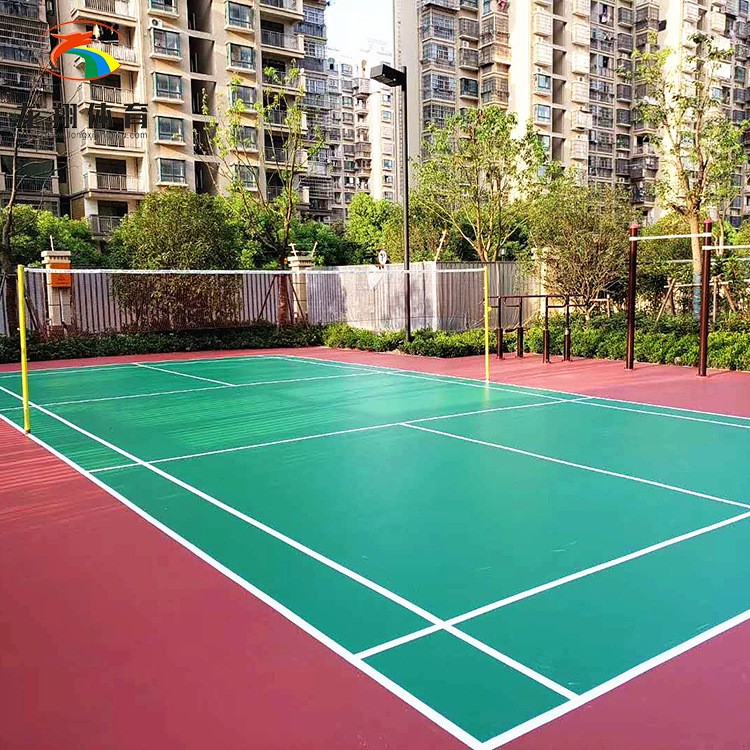
After the completion of the construction of the silicon pu court, although the silicon pu court material has the advantages of good sun protection and wear resistance, it is inevitable that there will be gaps when exposed to outdoor conditions and improper maintenance. This requires maintenance personnel to repair the gaps in the silicon pu stadium in time. The temperature seam of the silicon pu court is not only a repair work for the aftermath, but should be paid special attention when cutting. After the new cement foundation casting, it is necessary to cut the reasonable temperature expansion joint. The principle is to cut the square with no more than 6×10m. The temperature must be cut between the casting construction sections. The temperature seam width is 5~8mm and the seam depth is not less than 20mm (150mm). The thickness of the concrete base above the thickness is not less than 30mm) to ensure that the basic thermal expansion and contraction can be concentrated in the temperature seam and does not cause cracking in other parts of the foundation.
After the foundation is dried, apply special caulking glue to both sides of the temperature seam, and then squeeze the compressible foam into the temperature seam (reducing the compression of the base heat account to the surface of the caulking material to affect the surface effect), revealing The base part is polished with a hand-held grinder until it is level with the base surface, and then coated with a caulking glue on the surface of the temperature seam. The width is 80~100mm and the thickness is 1.5mm. It needs to be brushed in two ways to lay a thinner site (< 3mm thick), the ground surface of each side of the temperature seam (40~50mm) should be ground and lowered by 1.5~2.0mm.